隠れた世界企業 TRINC(浜松市、静電気除去装置の開発販売)
工場の大敵、静電気を退治
プラスチックの下敷きを布でこすって静電気をお越し、人の頭にかざすと髪の毛が逆立つ。
この状況を再現するため紙と木で作った小学校の理科の授業で使うような簡単な実験装置。
「見せてください。今からこの静電気を除去しますから」
技術ベンチャー、TRINC(トリンク)の高柳真社長は自社開発した静電気除去装置を片手に持ち、
実験装置に近づける。スイッチを入れて数秒、逆立って下敷きに吸い付いていた紙はしんなりと、すべて下に垂れた。
電子部品、液晶ディスプレーなどのガラス部品、自動車などの塗装工場では静電気が悩みの種だ。
静電気が原因で部品が故障したり、ガラスやプラスチックの表面にホコリがつき不良品が発生する可能性があるからだ。
静電気除去で独自技術を持つトリンクには、国内だけでなく海外の大手メーカーからの注文が来る。
昨年秋には韓国の液晶大手LGディスプレーから問い合わせがあった。1台50万円ほどする据え置き型の静電除去装置500台を納入する予定で、
これはトリンク同製品の1年間の販売量に相当する。
「世界の液晶メーカーは次と大型工場を新設していて、一番成長が見込める納入先だ」と高柳社長は胸を張る。
トリンクは1991年、ヤマハ発動機や通信機器メーカーの技術者を経験した高柳社長が電子製品の受託開発会社として創業した。
当初はファクシミリや携帯電話、車載センサーなど様々な製品の開発を手がけていた。
静電気除去にかかわるきっかけとなったのは古巣、ヤマハ発動機からの依頼だった。
ホコリが舞わない仕組みを開発
「ボート工場でホコリによる不良に悩まされている。何とかならないか」と知人に相談を受け、導入していた静電気除去機を調べると、改良の余地があると感じた。
静電気除去機はプラスイオンとマイナスイオンを高電圧で放射して、静電気を中和するのが基本的な仕組みだ。
従来機ではイオンを圧縮空気やファンで飛ばすために、静電気を取り除いてもホコリを巻き上げしまい、再び対象物にホコリが付着してしまうことがあった。
高柳社長は風を使わなくてもイオンを遠くへ飛ばすことを考え、プラスイオンとマイナスイオンの放射口を別々にする方式を独自に開発した。
放射口が同じだとイオン同士がすぐに結合してしまい、強い風力を使わないと遠くに飛ばせないからだ。
こうして開発した静電気除去機は「効果が増し使いやすい」と現場で好評となった。
高柳社長は「多くの工場で静電気の問題を抱えている。しかし、効果の高い製品は少ない。
これなら、うちのような技術ベンチャーでも参入チャンスがある。」と手応えをつかんだ。
そして、受託開発から自社製品の開発へと舵を切った。
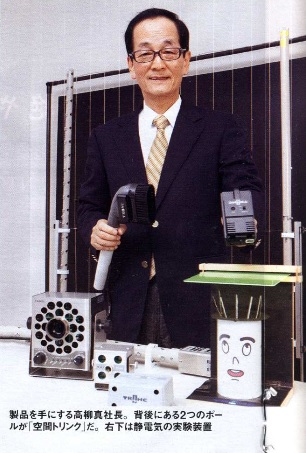
まずは、拳銃のように引き金をひいて対象物にイオンを吹きつけるガンタイプと、作業台の上に置くディスクトップタイプを発売した。
そして2002年、プラスイオンとマイナスイオンの放射器をポール状にして完全に分け、離れた場所に置くことで作業場全体の静電気を除去する
「空間トリンク」と呼ぶ新製品を商品化した。
これが地元、静岡県の塗装業者に納入されホコリによる不良率が下がったことが口コミで広がり、やがて大手メーカーからも問い合わせが来るようになった。
トヨタ自動車が塗装工程で空間トリンクを導入したことで評判となり、日立製作所の新幹線車両工場に納入するなど次々と実績を上げる。
しかし、実際の販売は一筋縄ではなかった。トリンクの営業スタッフはわずか10人程度。営業力を補うため商社などと販売代理店契約を結んでいるが、
キーエンスなど大手競合メーカに比べると力不足だった。また、独自技術で他社と違いを出しているものの、イオン放出による静電気除去という目に見えず
効果が分かりずらい製品を売り込むのは知名度のないベンチャー企業にとって困難を極めた。
そこで高柳社長が作った冒頭で紹介した実験装置。効果が分かりやすく商談相手の興味を引き付ける。製品の計測データを添え、製品を一定期間貸し出すぐに
サービスも始めたがそれでも現場担当者は導入に二の足を踏んだ。
「既に使っている静電気除去装置を入れ替えてまで、トリンクの製品を導入するにはリスクが大きい。もうちょっと検討したい」と決断を関野橋にされることもしばしまだった。
高柳社長は国内工場での導入が進まないことに業を煮やしアジアを中心とした日計企業の海外工場に目を向ける。「海外工場の方が現場担当者の権限が大きく、インフラなどもともとの環境が悪いだけに現状の改善に積極的なことが多い」(高柳社長)のその理由だ。大手メーカが生産拠点の海外移転を強化する流にも乗った。
トリンクは規模は小さいながらも売り上げを着実に伸ばし、2009年1月期には6億円に達した。海外販売が増収を牽引んし、売上比率は3割を占める。
海外企業への販売で低迷を打破
もっとも2008年9月のリーマンショック後に襲った経済危機で少なからず影響を受けた。自動車、電機、工作機械メーカーなどの多くの日本企業が減産体制を敷き、工場への設備投資を抑制した。風向きが変わったのは、昨年の秋。
「工場が再び稼働し、不況下で一段と生産効率の向上を目指し、静電気対策にも本腰を入れ始めた」と高柳社長は話す。
それでも業界の落ち込みは本格回復に至っていない。2010年1月期の売上高は前期比35%減の約4億円となる見通しだ。
状況を打開すべく高柳社長は日系企業だけではなく、海外メーカーへの販売を決断する。
実は、海外メーカーとの商談では過去に苦い経験がある。
トヨタでの納入実績を証明するため洗いざらい運用方法を教えてほしいと言われたからだ。守秘義務のため口外できないとする高柳社長に対し、食い下がる相手に閉口した。技術流失の危険も感じたのだ。
しかし、もはや躊躇している時ではない。
トリンクは国内で申請中を含め130の特許を持っている。取引先を慎重に選び、製品を外部に持ち出したり複製したりしないことを条件に販売契約を結ぶことにした。
海外メーカーからの受注に対応するようにしたのは昨年の秋からだが、積極的に営業をかけているわけではない。自社の成り立ちと製品、技術を紹介した英語の書籍を海外で販売し、トリンクに興味を持った企業からの連絡を待つ「受け身の営業」をしている。
この本は2007年に発行した高柳社長の著書『静電気・ホコリ[ゼロ]革命』(ダイヤモンド社刊)の英語翻訳版だ。
『Made in Japan』と題し、トヨタ工場に納入した実績を強調している。
その効果もあって、液晶大手の韓国LGディスプレーや台湾エイサーグループの友達光電(AUO)、電子機器の受注生産大手の台湾フォックスコンなどから
注文が入ってきた。アジアを中心に欧米にも販路を広げたい考えだ。
トリンクは、開発スタッフ10人で、製造は地元浜松のメーカー5社を中心に全て外注している。身軽な中小企業のままで次々と新製品を生み出し続けるのが
高柳しゃちょうの方針だ。
小さくても自ら世界大手を呼び込む。日本の大手企業とともに海外へ出る戦略から大きく舵を切ったトリンクは、今後の日本のモノ作りベンチャーの1つのヒントを指名して言えるだろう。